La monoscocca, ovvero il telaio della vettura, è il nucleo portante del primo prototipo elettrico (DP12evo) sviluppato da Dynamic PRC, il reparto corse automobilistico del Politecnico di Milano, è il telaio della vettura. Sulla stessa vengono montati tutti gli elementi che compongono compongono l’assieme
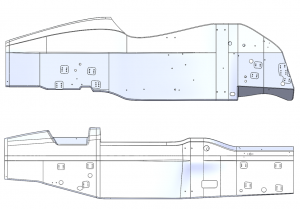
del veicolo, dalle sospensioni alle appendici aerodinamiche, dai pedali al pacco batteria e ai suoi condotti di raffreddamento. Come suggerisce il nome, il Team la produce in un pezzo unico, ottenuto mediante la laminazione di varie tipologie di materiali compositi, formati da matrice polimerica epossidica rinforzata con differenti fibre di carbonio.
Nuova categoria, nuove sfide
Dato che il Team ha deciso di optare per il cambio di categoria, da veicolo a propulsione endotermica a veicolo elettrico, sono stati completamente ripensati il progetto e la sua direzione di sviluppo. Questo ha influito molto sulla progettazione della monoscocca, in particolar modo sulle geometrie, che sono state ripensate creando lo spazio necessario
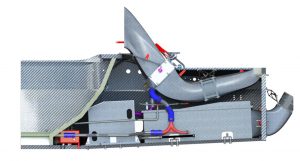
per l’alloggiamento del pacco batteria e dei componenti di erogazione della potenza. Inoltre, ridisegnando il profilo inferiore è stato possibile sfruttare un nuovo fondo a effetto suolo. Sono state rinnovate le zone di attacco delle sospensioni per alloggiare il nuovo schema push-rod.
Il rinnovamento di geometrie ha reso necessarie nuove simulazioni strutturali volte a ottenere la performance desiderata con la minore massa possibile. Il reparto Frame and Body, sezione Monocoque, ha condotto su di essa un lavoro di ottimizzazione della laminazione, che viene studiata seguendo due principi cardine: rispettare i limiti minimi di resistenza imposti dal regolamento e raggiungere i target di performance desiderati, analizzando la resistenza complessiva del pezzo e la rigidezza rapportata ai carichi che subisce e alla massa finale.
Leggera, ma sicura
Il regolamento delinea una serie di zone della monoscocca che risultano fondamentali per la sicurezza dei piloti e dei componenti ad alto voltaggio, che costituiscono la powertrain del prototipo. Di queste aree fanno parte i supporti dei rollbar di sicurezza e della struttura di
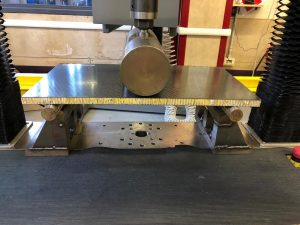
assorbimento degli impatti, i punti di attacco delle cinture, i pannelli a lato e sotto il pilota e il vano batteria. È infatti fondamentale che in caso di incidente sia garantita la salute del pilota e siano evitati danni ai componenti sopra citati, che se intaccati potrebbero innescare incendi ed esporre a rischi di folgorazione. È infatti obbligatorio per queste aree condurre test sperimentali distruttivi in laboratorio su pannelli che presentano la medesima composizione e costruzione. In questo modo si ricavano la rigidezza flessionale e lo sforzo massimo che possono sopportare, da confrontare con i valori minimi richiesti per ottenerne l’omologazione finale. I progettisti che se ne occupano conducono una serie di simulazioni a elementi finiti che precedono i test mirate a
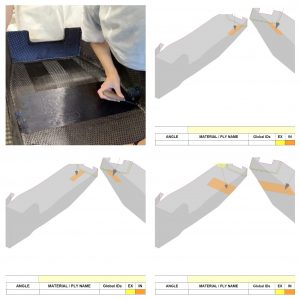
individuare i pannelli con la migliore rigidezza specifica, cioè la rigidezza rapportata alla densità del pannello.
Per quanto riguarda la resa strutturale rapportata ai carichi che provengono dalle sospensioni, si fa in modo che a seconda della zona della monoscocca cambi il layup di laminazione, cioè la sequenza di posizionamento dei singoli strati e la loro orientazione nel piano. Vi sono zone con numerose “pelli”, ovvero i singoli strati di materiale, e con core di spessore elevato, e vi sono invece altre zone, notevolmente meno sollecitate, costituite da un minor numero di pelli e da core più sottili o meno resistenti. Per poter individuare la laminazione ottimale vengono condotte svariate analisi che sfruttano il metodo a elementi finiti, nelle quali vengono considerati i casi più critici che si presentano in esercizio. Inizialmente la monoscocca viene riprodotta utilizzando le laminazioni omologate in laboratorio per le zone regolamentate e laminazioni utilizzate negli anni precedenti per le altre zone. Confrontando i risultati ottenuti con i target prestabiliti, tra i quali la rigidezza torsionale, la deformazione massima dei punti di attacco delle sospensioni e il fattore di sicurezza nelle aree più sollecitate, si conduce un lavoro di ottimizzazione
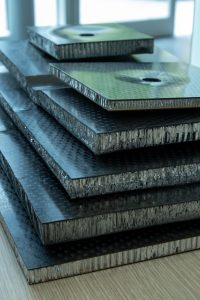
della laminazione per raggiungere il target desiderato. Durante questa fase vengono individuate le zone che necessitano di maggiore rigidezza, le quali vengono irrigidite con l’utilizzo di materiale rinforzato con fibre unidirezionali ad elevato modulo elastico. Al contrario, nelle zone che risultano eccessivamente rigide rispetto alle sollecitazioni che devono sopportare, si riduce lo spessore del core oppure si cambia il materiale che lo costituisce, utilizzandone uno meno rigido e di densità inferiore. In alternativa, viene ridotto il numero di pelli che compongono le lamine di fibra di carbonio. I progettisti potrebbero anche decidere, se necessario, di irrigidire una zona che risulta già omologata secondo il regolamento, nel caso in cui l’aumento di massa comporti un miglioramento considerevole delle prestazioni complessive.
Una monoscocca in evoluzione
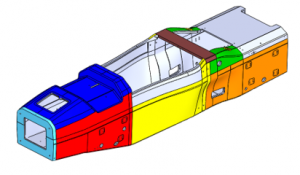
La sequenza finale di laminazione è così composta da numerosi differenti layup, studiati per rientrare all’interno dei parametri regolamentari minimi e ottenere la performance ottimale desiderata, minimizzando la massa complessiva della monoscocca. Essendo il primo prototipo elettrico, i progettisti hanno adottato una direzione conservativa riguardo l’utilizzo degli spazi al suo interno.
Gli sviluppi futuri riguarderanno infatti un’ottimizzazione delle geometrie, per ridurre il più possibile lo spazio inutilizzato tra i componenti al suo interno e le pareti e quindi la sezione trasversale, con notevoli benefici a livello aerodinamico oltre che a livello di massa.
di Jacopo Muzio – Ufficio Stampa DynamiΣ PRC