Sfruttare i materiali di stampa 3D FDM ad alte prestazioni per sostituire la manifattura tradizionale per una serie di applicazioni di produzione complesse: ci si è messa Due Pi Greco, con l’ausilio di Stratasys.
Dopo aver implementato con successo la stampa 3D di quest’ultima, l’azienda specializzata nella progettazione, ingegnerizzazione, prototipazione e nella produzione di parti e componenti funzionali sta ora utilizzando i materiali Stratasys FDM come driver principale per estendere l’utilizzo della fabbricazione additiva ad altre applicazioni.
Oggi, Due Pi Greco sta sfruttando positivamente le diverse caratteristiche ad alte prestazioni del Nylon 12CF FDM, della resina ULTEMTM 9085, del materiale solubile ST-130 e dell’ASA di Stratasys, per nuove applicazioni di produzione all’interno di diversi settori industriali rese disponibili dalla fabbricazione additiva in alternativa ai più costosi metodi tradizionali.
Da una caldaia stampata in 3D per Zoppas…
Come spiegato in una nota ufficiale da Diego Pagnan, fondatore e titolare di Due Pi Greco: «La gamma diversificata di materiali di produzione Stratasys ci permette di sviluppare alcune applicazioni innovative per i nostri clienti. Ad esempio, recentemente abbiamo progettato e prodotto una caldaia stampata in 3D per Zoppas, fornitore globale di sistemi di riscaldamento per uso domestico e industriale».
Questo è stato possibile grazie alla resina ULTEMTM 1010, l’unico polimero capace di resistere a temperature fino a 216 °C. Allo stesso modo, ultimamente, sempre Due Pi Greco ha stampato in 3D due parafanghi delle ruote posteriori per un produttore leader mondiale di macchine agricole.
Sfruttando la maggiore durata e l’alta resistenza ai raggi UV del materiale ASA, l’azienda è stata in grado di sostituire il tradizionale ABS risparmiando sui costi.
«Senza le proprietà avanzate di questi materiali, semplicemente non saremmo stati in grado di sfruttare la grande efficienza offerta dalla fabbricazione additiva per questo tipo di applicazioni di produzione complesse», ha aggiunto Pagnan.
Partendo dalle quattro stampanti 3D FDM di Stratasys già in suo possesso, l’azienda ha appena fatto un investimento acquistando una Fortus 380 mc Carbon Fiber Edition (CFE) dal partner di Stratasys, Energy Group.
Il fattore determinante per la scelta è stato il materiale Nylon 12CF FDM, un composito avanzato per la stampa 3D che integra un 35% di frammenti di fibra di carbonio.
Secondo Pagnan, le proprietà del materiale hanno offerto al team una maggiore capacità di risposta rispetto a una crescente richiesta di prestazioni elevate da parte di nuovi clienti, consentendo loro di accettare una maggiore quantità di incarichi.
«Le stampanti Fortus 3D sono sempre state un nostro cavallo di battaglia in termini di affidabilità, ma abbiamo deciso di investire nella versione in fibra di carbonio perché abbiamo ritenuto che fosse la migliore alternativa alla lavorazione CNC di costose parti metalliche – afferma il numero uno di Due Pi Greco –. Utilizzando il Nylon 12CF FDM, siamo in grado di stampare in 3D parti con prestazioni simili a quelle prodotte con processi di lavorazione CNC. Questo ci consente un risparmio significativo in termini di tempo e di costi rispetto ai metodi convenzionali di produzione con i metalli. Inoltre, la qualità dei pezzi ha suscitato grande sensazione anche tra i nostri clienti aprendoci nuove opportunità commerciali».
… a un airbox per il motore di una monoposto da corsa!
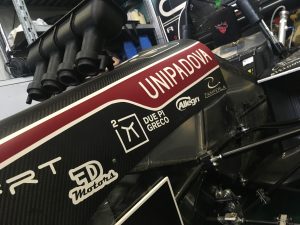
Questi vantaggi sono ben esemplificati da un recente progetto di collaborazione con l’Università degli Studi di Padova, in occasione del quale Due Pi Greco ha stampato in 3D un airbox per il motore di una monoposto da corsa destinata a gareggiare in Formula SAE.
L’azienda ha aggirato i lunghi tempi di lavorazione e gli alti costi della fabbricazione tradizionale in fibra di carbonio stampando in 3D l’intero airbox con il Nylon 12CF FDM, consentendo al team di ottenere un risparmio significativo in termini di costi e di tempo. La velocità con cui il team ha potuto stampare in 3D la parte è stata fondamentale per poter iterare il progetto e testarlo in pista per una prestazione ottimale.
Questo aspetto è stato determinante anche in un altro recente progetto per un marchio leader del ciclismo italiano, in cui il team ha utilizzato la Fortus 380 mc CFE per ottimizzare la progettazione e la realizzazione di una sella per biciclette di gamma alta. Secondo Pagnan, il cliente ha riferito che il risultato ha superato di gran lunga le aspettative in termini di finitura delle superfici e resistenza.
Facile intuir il commento finale: «Agli inizi della nostra attività, operavamo prevalentemente come fornitore di servizi di stampa 3D per soddisfare esigenze di prototipazione. Tuttavia, l’utilizzo delle stampanti 3D Stratasys attraverso tutto il processo di sviluppo ci ha permesso di comprendere meglio il notevole potenziale della fabbricazione additiva per la produzione. Questa esperienza ha cambiato completamente la nostra visione e l’approccio alla progettazione e alla produzione, e la fabbricazione additiva adesso svolge un ruolo fondamentale nel processo di sviluppo del prodotto».
Per Giuseppe Cilia, responsabile vendite di Stratasys per l’Italia: «La sfida più grande per gli specialisti di design e produzione oggi è quella di fornire soluzioni di alta qualità dalle massime prestazioni, con tempistiche stringenti e budget contenuti. Aziende come Due Pi Greco sono un esempio significativo di come la fabbricazione additiva FDM di Stratasys possa aiutare ad affrontare questa sfida a testa alta. Detto questo, non ci adagiamo sugli allori, perché continuiamo a lavorare a stretto contatto con i nostri clienti per ottimizzare ulteriormente i nostri materiali ad alte prestazioni per consentire di estendere la fabbricazione additiva a nuove aree di produzione».